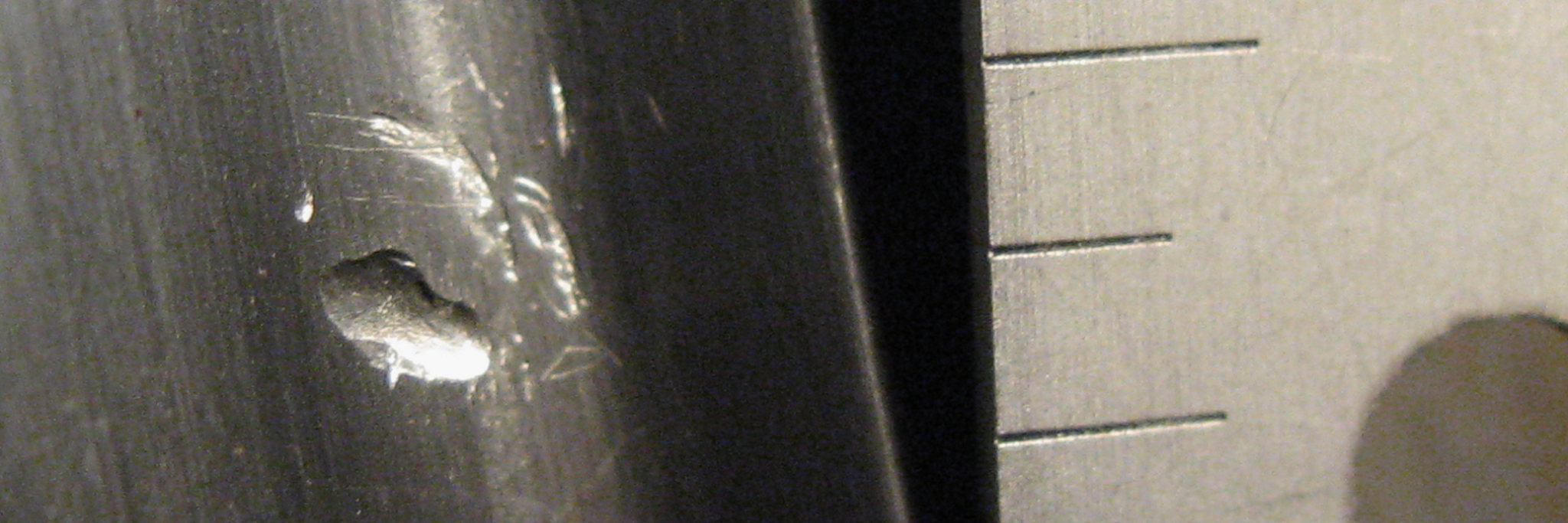
Inspection Requirements
Div. 1
- RT Required to varying extents based on user definition, service conditions, and material thicknesses
- Full RT, spot RT, or none is allowed
- Joint efficiency changes with RT Scope (thicker by 15% if it’s not RT’d)
- Increased design margins and design rules account for, in some cases, no inspection
- TFES RTs 100% buttwelds , MT of nozzle welds by standard, MT some other miscellaneous welds
Div. 2 (code driven)
- RT or UT 100% welds
- Magnetic particle inspection of butt welds and nozzle welds
- UT of 100% nozzle welds
- MT of weld bevels
- Wet MT all welds after hydrotest (in fatigue service)
- Other attachments welds subject to UT/MT
- All code compliant NDE prior to PWHT to make sure anything is repaired prior to PWHT
Material Testing
Div. 1
- Material must be tested to the same heat treatments as the vessel
- Exemption for standard flanges/fittings
- Exemption for most “normal” carbon steels ex: SA516-70
Div. 2
- Material must be tested to the same heat treatments as the vessel
- Exemption for standard flanges/fittings
- Test specimens for other vessel material must be tested in the heat treated condition – ordered with SPWHT (simulated post weld heat treatment)
NDE by Material Suppliers
- UT plate and forgings 2” and thicker in raw condition
- MT forgings after finished machining
- MT/UT of bolting based on thickness
Fatigue Analysis
- Cyclic operations conditions specified in UDS
- All vessel components must be evaluated for fatigue (would be a document of calculations)
- Screening performed per 5.5.2
- Fatigue analysis required, yes or no?
- If yes, div 2 provides procedures for the fatigue analysis
- FEA can be used and may be necessary to derive stress results for the analysis but it’s not always necessary
So you’re on a budget? Check out these 5 tips to save money on your next Slug Catcher Project.
As a leader in Slug Catcher design, here are some guidelines every engineer should know.
Understanding the separation methods for your finger-type slug catcher.
WHY US
Taylor Forge Engineered Systems
has continued the reputation of traditionally dependable products
to a variety of industries.
Integrity
We don’t compromise our practices and we won’t cut corners.